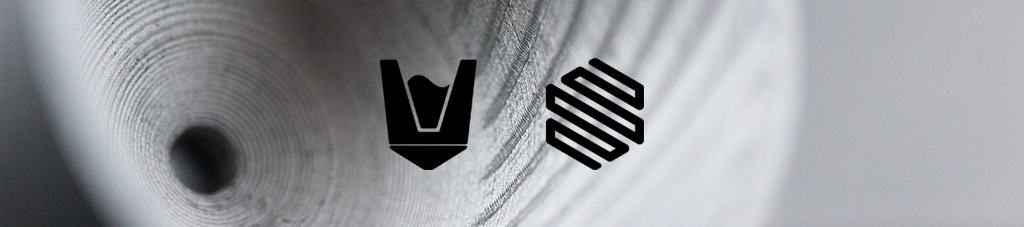
CONGRATULATIONS MATTIAS, WINNER OF OUR METAL X CHALLENGE 2021
During the summer, 3DVerkstan together with Markforged announced a competition for Swedish students with an interest in additive manufacturing. The challenge was to design a part suitable for printing with Markforged’s ADAM technology, in the Metal X printer. We received designs of many great applications, and we consider all our top 5 finalists winners – to be acknowledged and receive their design printed in copper. The winner of the first prize, and happy new owner of an Onyx One 3D-printer, is Mattias Dünkelberg Valenca who is doing his B.S. in Electrical Engineering at KTH in Stockholm. Mattias stood out with his innovative design of a homopolar generator disc! We had a chat with some of the people behind the competition, and of course with Mattias himself.
First up, Patrik and Kyle from the jury, what were your expectations for the Metal X Challenge?
In one way I consider students to be untouched with free minds and undisturbed creativity. So I think I had pretty high expectations to be honest. I was expecting the students to really read up on the design guidelines to get inspiration. And the top 10 applicants had really put a lot of time and effort into their designs! The fact that I personally want to have many of the top 10 designs for myself really shows the success with this challenge, answers Patrik Rosén, sales manager and application engineer at 3DVerkstan.
Kyle Mason, regional sales manager at Markforged, adds: To be honest, I didn’t have many expectations. We tried our best to limit the constraints and rules of the competition as much as possible and let their minds run wild. We really didn’t know what we’d get. Consistency is often boring and we were definitely not bored with the designs we saw! I was pleasantly surprised by the wide range of parts from fishing rod assemblies to electrical components.
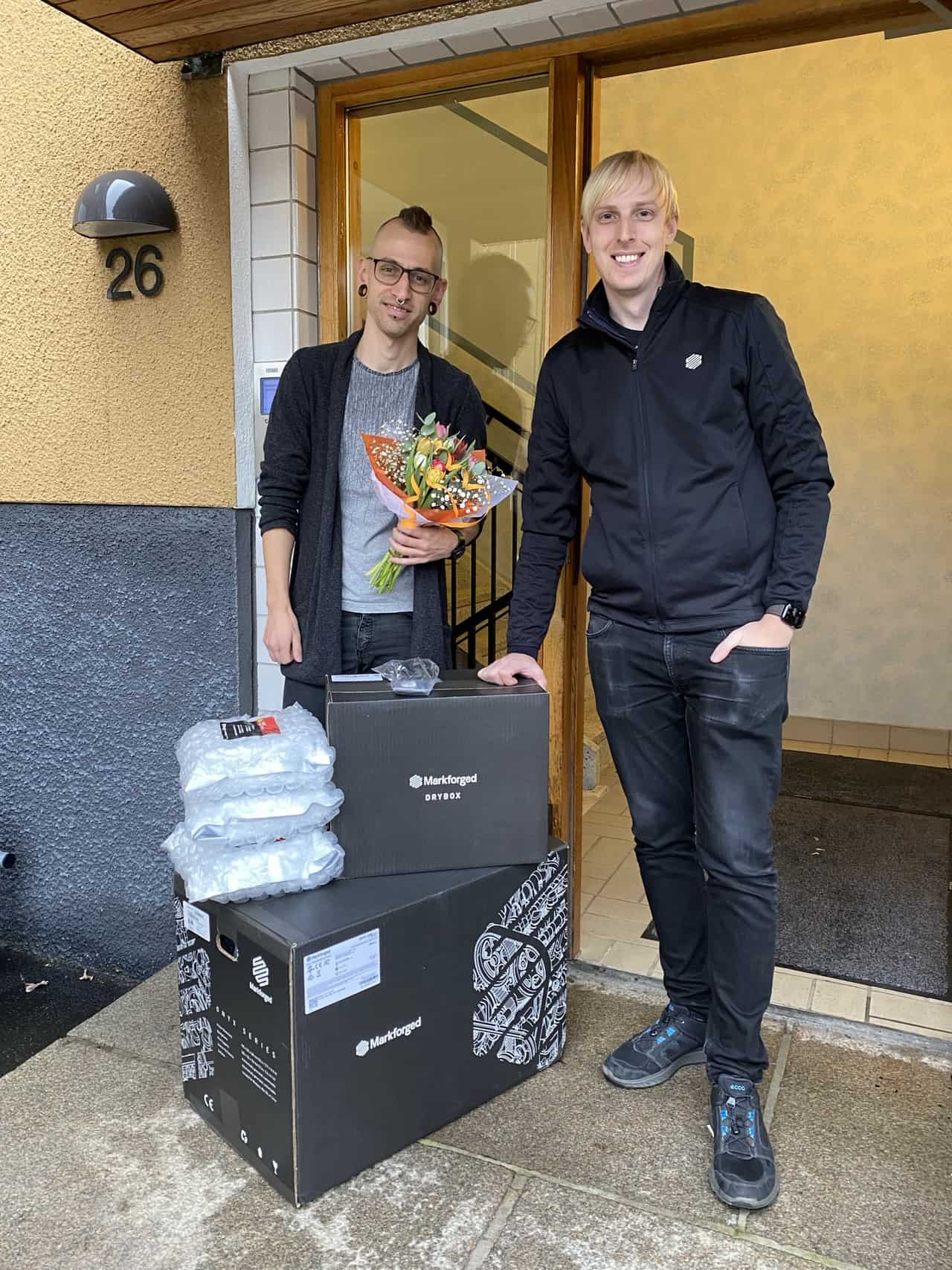
Mattias, left, receiving his prize from 3DVerkstan sales rep Linus.
What were you looking for in a winning competition entry?
We were looking for a design where it was clear the participant did their homework. Of course, we wanted designs built specifically for 3D printing and that leverage the strengths of the technology. However, each additive process has its nuances and that’s where our focus was. The devil was in the detail of our design guide! Additionally, creativity always plays a role. We were particularly interested in parts that were relevant to feasible, real life applications, explains Kyle.
Tell us about your thoughts on Mattias’ winning design!
Mattias' design really attracted our attention at an early stage. The design is pretty much impossible to manufacture in other ways – or at least way more expensive. His presentation in the “shark tank” was really good and answered our initial questions. The huge amount of E-bikes in Sweden currently makes the application extra interesting as well, says Patrik.
Mattias’ submission was a passion project. It was something that was relevant to his everyday life. We rarely get the opportunity or have the time to engineer and innovate on items that could impact our own lives, and that hit home for me. Also, electric vehicles are a hot topic these days and it’s exciting to see the momentum picking up with the next generation of engineers, Kyle concludes.
Congratulations Mattias, winner of the Metal X Challenge 2021! How did you come up with your winning design?
The thought of this design originated from me cycling up a lot of hills – initially with a regular bike and later with an electric one – which made me think about the gravitational potential energy stored in the bike that could be put to use during the long downhill distances. How could one make use of all that stored energy? And couldn’t it be used to recharge the bike’s battery? In practice there’s of course a lot more electrical control systems and mechanical design that need to be addressed before the part can become a functional product. But I figured that this potential energy, at least on a conceptual level, should be possible to utilize to generate electricity.
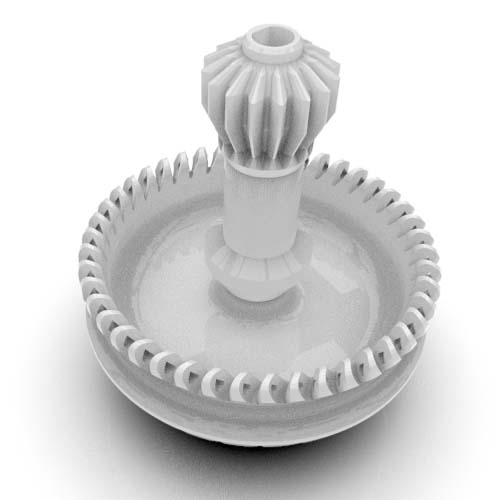
What was the result?
My submission was the electrical induction part of a homopolar generator, also known as a Faraday generator. The 3D-printed part, that is made out of copper, would be mounted in a gearbox angled towards the wheel of a bike to provide power to a battery charging circuit while riding the bike down hill. The generator works by rotating the copper part in a static magnetic field, which will induce a current flowing between the inner- and outermost points of the disk, as described by Faraday’s law of induction. The generator is able to generate high currents, even if the potential difference on the points of the disc are not very large. The amount of power generated is determined by the rotational speed of the disc and therefore you want the disc to be able to rotate as fast as possible. The special possibilities for intricate geometries that are available for 3D-printed metal parts, allowed me to design cooling fins that allows for greater airflow at the surface of the copper. This will hopefully increase the thermal conductivity of the designed part, which normally can become quite hot due to eddy currents.
What does the future look like for you?
Right now I’m halfway through my Bachelor of Science in Electrical Engineering at KTH Royal Institute of Technology. Once that's done, we’ll have to wait and see what I will choose for my Master's programme. Currently I’m leaning towards studying medical technology, which includes electronics and biomechanics. In this field there’s definitely great opportunities to incorporate 3D printing and 3D scanning, considering customizable prostheses, implants and so on. I think that the usage of such manufacturing technology will grow a lot in the coming years, so it would be really interesting to choose that field to combine my interest in additive manufacturing, medical tech and electrical engineering.
Considering that you’ll soon receive a Markforged Onyx One 3D printer, what’s the first print you will start?
I’ve actually designed another part for my bike – an adapter for the hub. I did print it once before, but now it will be exciting to print it in Onyx. It will probably need some redesigning and it’ll be fun to see how it turns out. I might produce it for other people I know that are also interested in cycling. So that’s the first thing I’ll do, and then we’ll see. I’m above all keen on just testing to see what limitations the material has – how much it can handle and how tough it is.
We’re looking forward to hearing more from Mattias. Congratulations again and good luck!
The top 10 designs of the Metal X Challenge
Together with Markforged, a leading producer of industrial 3D printers and software, we at 3DVerkstan hosted a technical design competition aimed at Swedish university students. The challenge was to create a functional and innovative 3D-designed model suitable for metal 3D-printing with Markforgeds ADAM-technology.
It has been a pleasure to see all the amazing designs sent in to us during the competition. After considering the capabilities of the designs, as well as the limitations of the Metal X-system, and following the guidelines set, we have chosen our top 10 designs and present them here.
More information on the selected winner and interviews will follow. The Universities will also benefit from the competition with a great opportunity to invest in Markforged printers. All in favour of the students to ensure they are prepared for the future workforce.
Homopolar generator disc
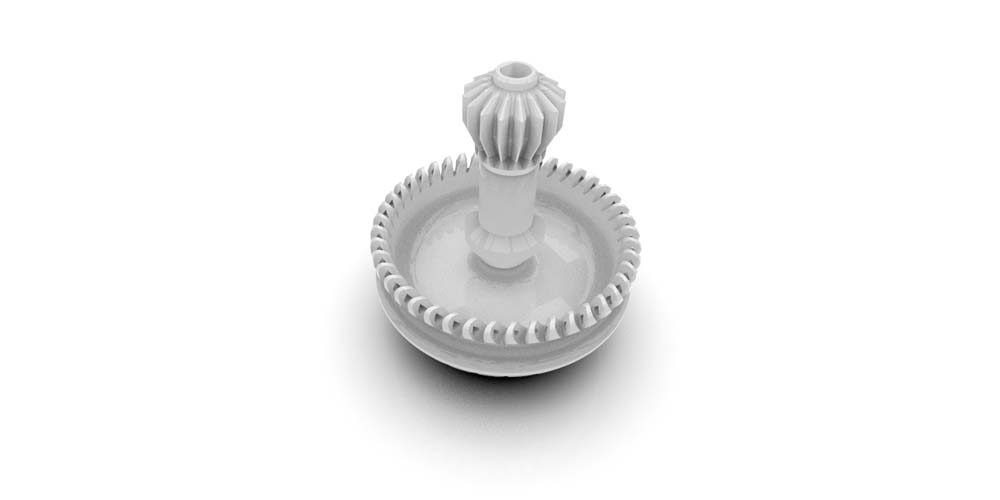
"My Metal X Design entry would, if printed, provide me with the essential part to construct a homopolar generator, also known as a Faraday generator. The device would be mounted in a gearbox on a bike to power battery charging with relatively high current while riding the bike. The part needs to be made out of copper in order to conduct current as the disc rotates in a static magnetic field. The special possibilities for intricate geometries that are available for 3D-printed metal parts will allow for greater air flow at the surface of the copper, which will increase the cooling of the metal, which normally can become quite hot due to eddy-currents.
The biggest challenge when designing this part was finding the "sweet spot" between the limitations of the printer and the desired form. I believe that I found a design that both meets my needs for the part but also shows the great possibilities of the printer. "
Heat exchanger
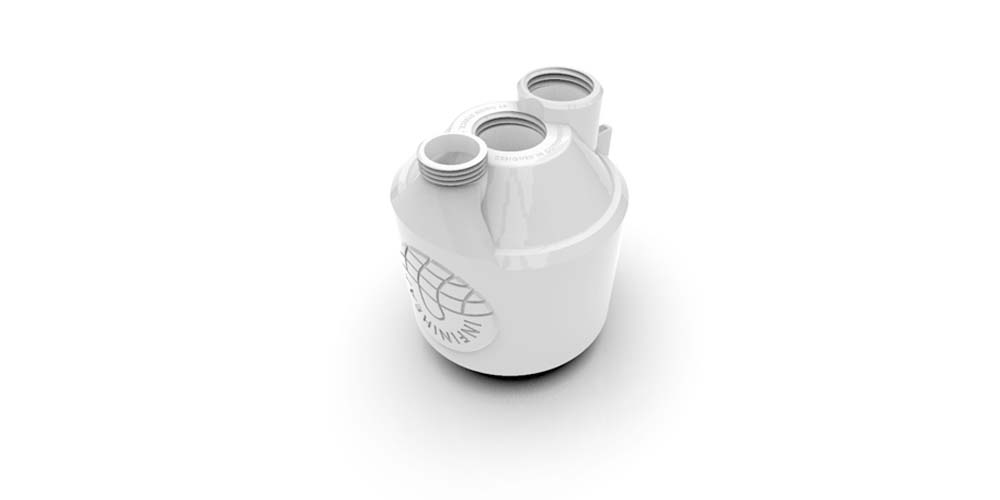
"This concept was inspired by high-end heat exchangers produced with LB-PBF/EBM for aerospace. By using the same principles in low-end consumer products, water heaters across the globe could be made more sustainable. This part is the first step into utilizing metal additive manufacturing at mass-scale to create water heaters that are more energy-efficient than existing products and has a smaller footprint in production.
The model was developed to maximize the potential of the Markforged Metal X and copper material to produce an energy-efficient water heater that is easier, safer and cheaper to produce than with additive manufacturing competitors. The model has been designed with wavy internal fins to ensure Metal X printability while still pushing the limits with its thin walls and intricate details. "
Compact cylinder
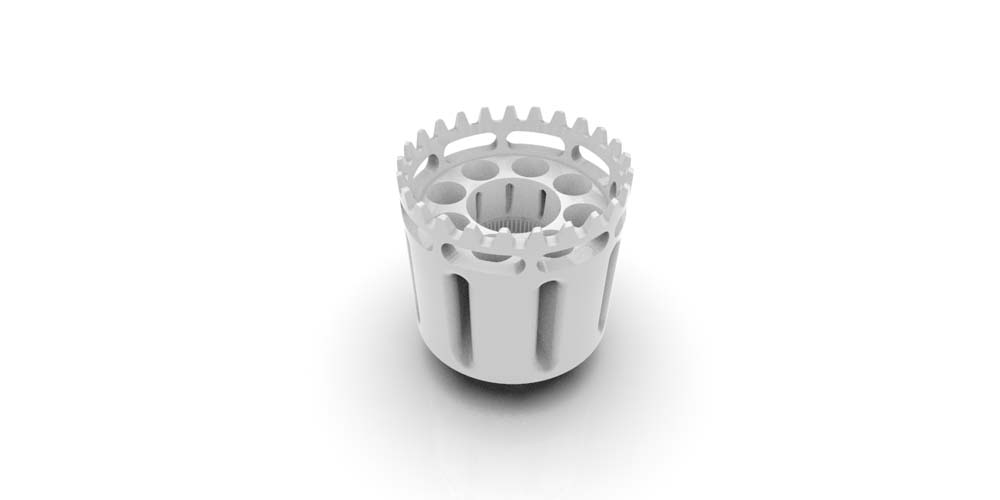
"Compact main cylinder of a rotary compressor, with special feature like internal cut out for weight reduction and air channels for cooling. Also includes gear features for gear drive 1 stage compressor fan. The light weight design and compact part adds up to an efficient small compressor. Additive manufacturing with the Metal X makes it extremely light and easy to manufacture."
Turbine rotor
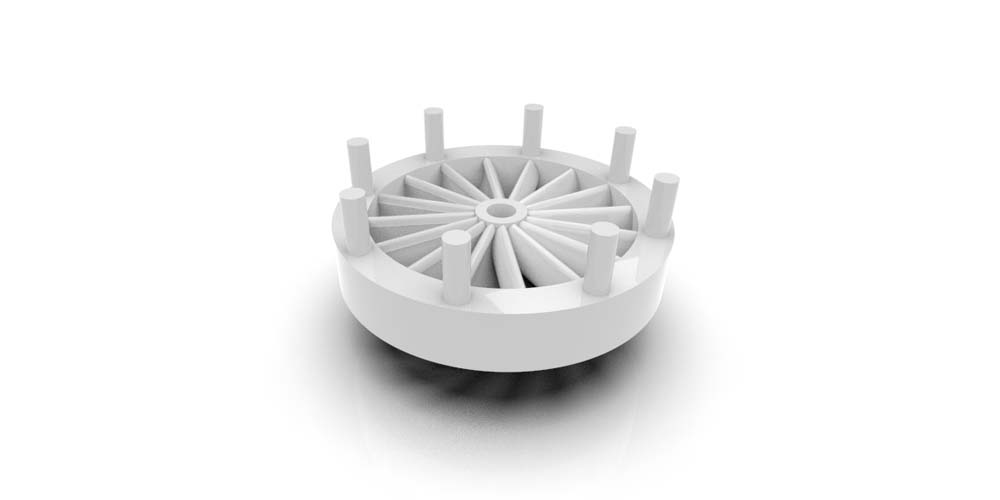
"I have made a Turgo turbine with an integrated generator where the spool holders will be built in the lower turbine and holes for the magnets are made on the upper turbine. The rotor and stator will therefore be built inside the turbine. Rotating in two opposing directions. Taking advantage of the energy that isn’t used by the first turbine and making the lower one rotate in the other direction.
This can, if developed further, make turbines cheaper as you don’t have to build both a generator and a turbine. The lower turbine would need a slip ring to transfer the electricity out of it. If this turbine is positioned under water more work would have to be done making sure it is waterproof. Which could be done. With slower currents it might be possible to reach 50 hertz without having to use massive gearboxes. I think that this is a creative piece of technology that combines the generator with the turbine."
Garden wind turbine
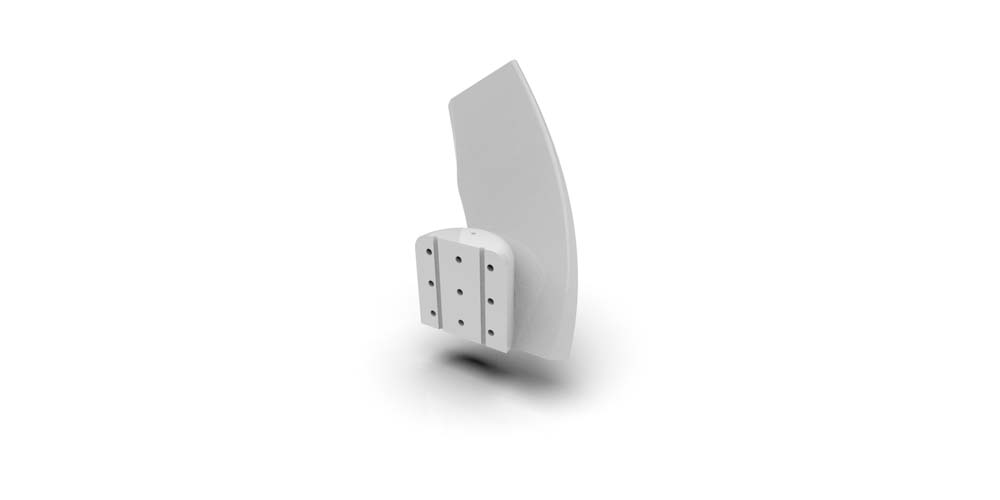
"What I am presenting is a model of a garden turbine. The idea started from observing some pinwheels, thinking how nice it would be to use them to produce small amounts of electricity for household purposes. I began to think about how such an object could be made and what shapes it should have. Their shape and color is the result of research done with the aim of getting a shape that can blend in among the flowers and plants, this should be an object that should not be conspicuous. In fact, the shape resembles that of a flower bud ready to reveal its first petals, only in this case the petals, so to speak, serve to capture the energy of the wind. The object should be made of aluminium so that it is neither too heavy to be moved by the wind, nor too light to be easily damaged by the weather. The concept is based on having a series of these prototypes connected together through electrical cables that will all converge in a generic transformer. In this way, the surface of a normal courtyard, or a flat roof could be used to derive/actuate power consumptions from public networks."
Cooling Head
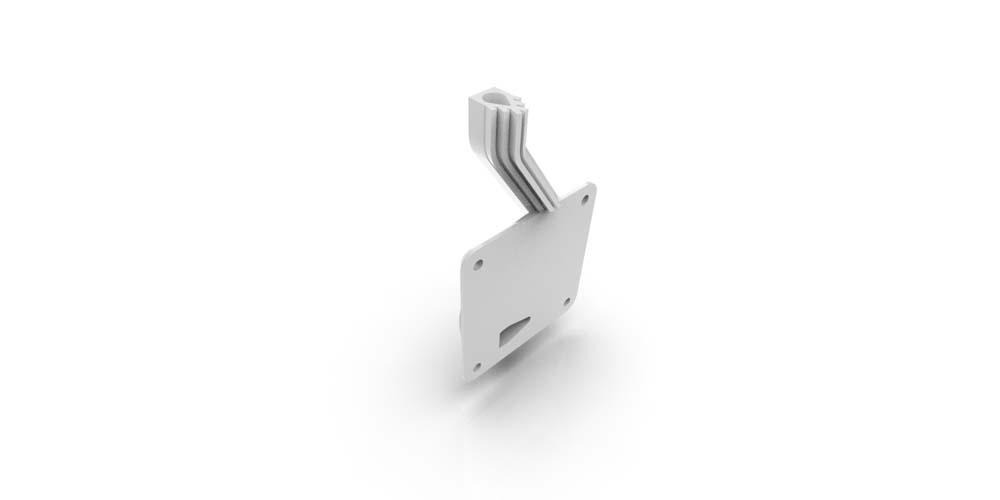
"This is a cooling head for the Raspberry Pi 3. A common problem with the raspberry is that it overheats quickly and throttle down processor performance even with heatsinks attached. This cooling head with fan mounting should provide good heat dissipation even on low fan rpm, it mounts to the two processors with heat conductive tape.
This part have to be made out of copper to transfer heat and printing it is almost the only possible way of producing it because of the internal air channel."
Johan Peteri, Umeå Universitet
Alcohol burner nozzle
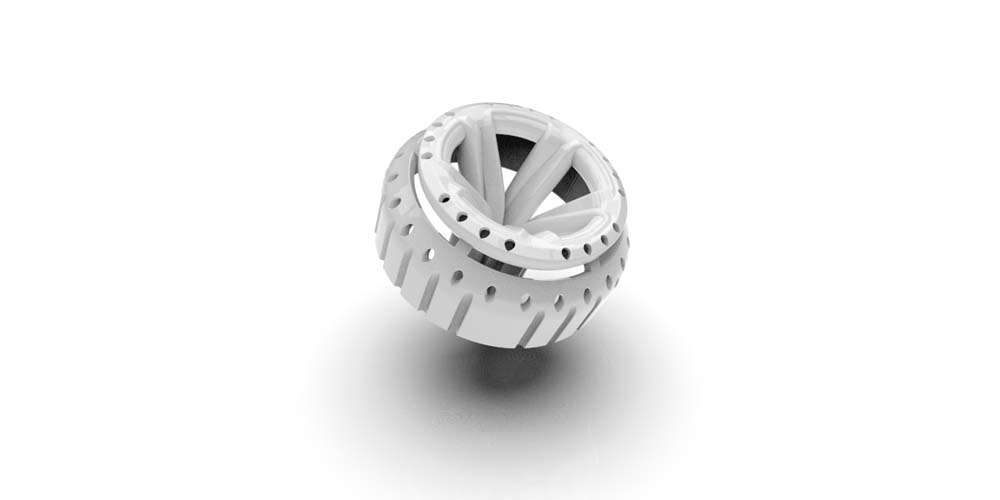
"I have created an add-on for an alcohol burner of the type used in Trangia's camping stoves. The design is created with tubes that are meant to contain the wick, which gets heated by the flames. As a result, the evaporation of the alcohol is increased, as well as the efficiency and heat output of the burner. The process started with brainstorming and sketches, followed by intensive 3D-modeling to find the final shape.
The main issue has always been optimizing the design so that minimal support is needed. Also, securing the holes in such a way that they will print properly. I solved this by deciding that no angles could be lower than 45 degrees. This part should be printed in metal because previous attempts at this type of construction have failed when it comes to production costs due to a big need for human workforce for final assembly. Therefore, there aren't any current products on the market like this due to the high production cost. All of that is solved by getting a ready made product that is ready to ship."
Daniel Forsberg, Mittuniversitetet
Impeller housing
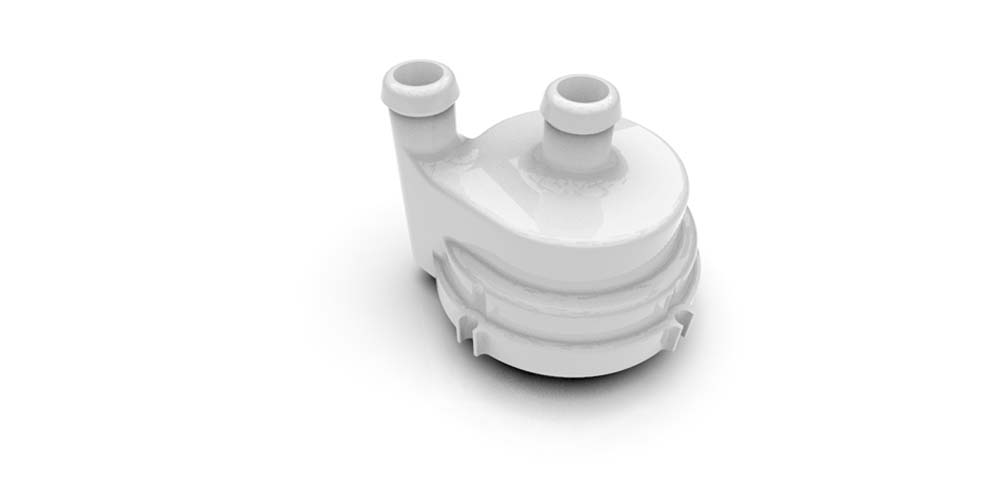
"Reengineered replacement impeller housing for an old pump. The old housing seemed to be injection moulded plastic, so I had to make a few changes to fit this style of manufacturing instead. I started out with a design that was quite similar to the old one. However, that design required a lot of support material and would be quite expensive to 3D-print, $77 according to Eiger. My focus for this design has been to minimize support, minimize material and to minimize cost. In order to minimize support, the outlet is turned 90 degrees and is now pointing upwards instead of horizontally. This also allows for the horizontal channel to be printed in a teardrop shape instead of a circular one, further reducing the amount of support needed.
The final design is about $22 cheaper than the initial design and print time and material is reduced significantly. Much cheaper than buying a completely new pump which can be up to $500. "
Erik Ljungberg, Kungliga Tekniska Högskolan
Stainless steel knob
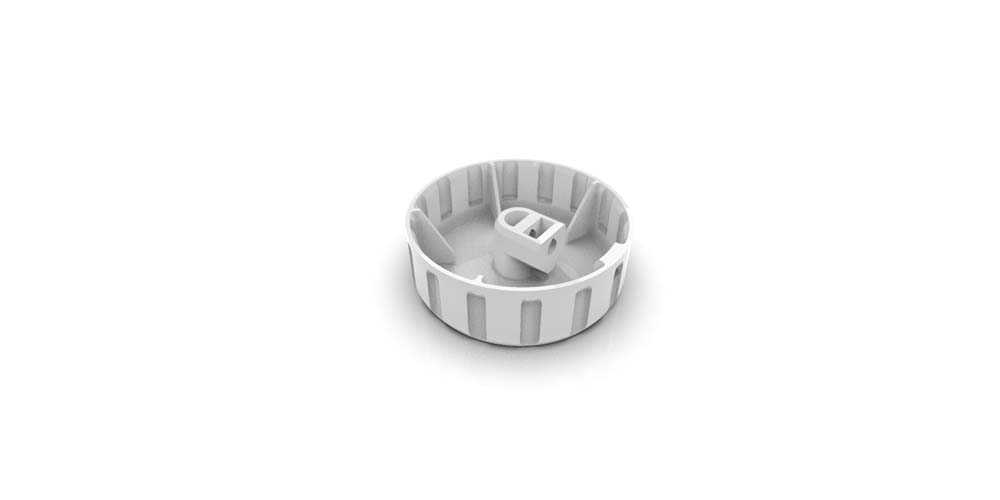
"This stainless steel knob is designed specifically for 3D-printing. It can be printed with zero support materials due to all details are designed with 45 degrees angles or less. The knob is cleverly designed with minimum amount of material usage. I have leveraged the freedom of design in 3D-printing to make a very good looking design which is usually difficult to do with other manufacturing methods. After printing, washing and sintering the knob can be used directly, so there is no need for taping the thread and post processing. This 3D- printed knob will be cheaper than a CNC machined one with about $3. The cost of the knob in Eiger is about $14 in comparison with CNC machined one that costs about $17."
Anas Tabbah, Jönköping Universitet
Miniature Hybrid rocket
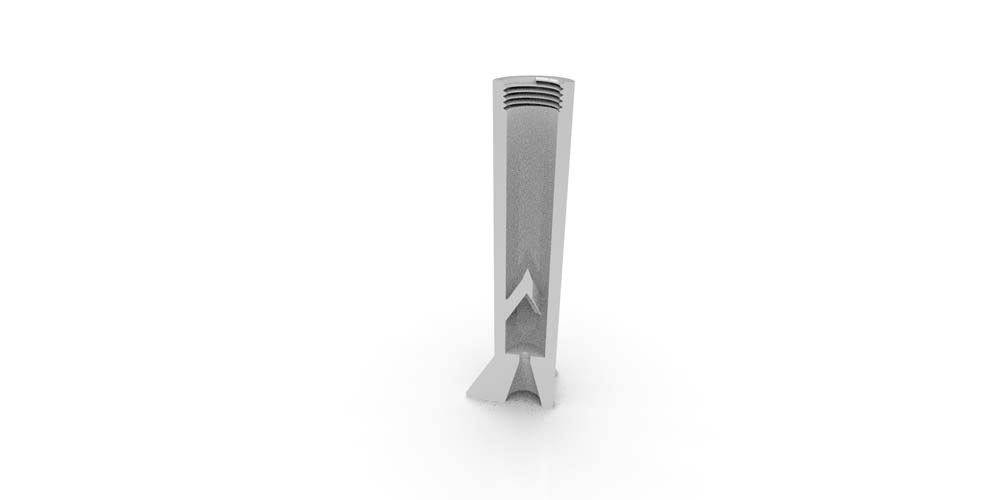
"Hybrid rockets are difficult to test and optimize. Testing is essential to make a good hybrid rocket. Students studying rocketry can learn a tremendous amount if they are able to use metal 3D-printers to rapidly prototype rocket engines. Using the Markforged Metal X alongside this rocket design will enable students to test different engine configurations and propellant mixtures.
Part consolidation of the fins, nozzle, combustion chamber, body tube, piercer results in a cheaper solution compared to making those parts individually. With the piercer inside the body tube, the part is not manufacturable via traditional measures. Using Inconel 625, the 3D printed structure will be strong enough to resist the combustion of nitrous oxide and paraffin wax "
Education and Research Bundles
Prepare the next generation of industry leaders with Markforged
STEM-focused schools and universities have two main objectives when educating their students. First, they seek to build a strong backbone of technical knowledge through theory-heavy classes. Second, and perhaps more importantly, they provide a place for students to learn and practice real job skills before joining the workforce.
Investing in Markforged systems is the best way for your students to develop additive manufacturing expertise
in an educational setting. Our Digital Forge platform is widely adopted — more than 12,000 connected machines worldwide — and features industry leading metal and composite 3D printing technology. Even more importantly, we’ve developed a curriculum that your teaching staff can integrate into their lessons. Our machines are reliable, need minimal maintenance, and exist to make functional parts for you.
Elevate your 3D printing profile with the most advanced 3D printers Markforged offers, powered by the Digital Forge platform. Featuring Blacksmith, our breakthrough inspection software, in addition to metal and composite printing, the Advanced Package will empower your students to learn the full cycle of manufacturing: design, fabrication, inspection, and implementation. We’ve also included some tools to further hone your additive skills: Markforged University and a success plan.
CONTACT US FOR A DEMO OR MORE DETAILS ON THE DISCOUNTED BUNDLES: info@3dverkstan.se