Fritid & Vildmark
Tuffa krav uppnådda
med Fuse 1
I Piteå hittar vi utelivs-ambassadörerna Fritid & Vildmark – en verksamhet med gedigen erfarenhet av att ge service för friluftsintresserade människor. Ända sedan start har mottot varit respekt- och ansvarsfullt brukande av vad naturen erbjuder, och idag har Fritid & Vildmark norra Sveriges bredaste sortiment för jakt, fiske och uteliv. Moritz Isaksson kontaktade oss på 3DVerkstan för att få support till utvecklingen av en ny produkt – och tillsammans tog vi fram en ny kolvmodell som endast genom 3D-printing kunde uppnå de krav som önskades.
Moritz Isaksson arbetar med att fördela, utveckla och bearbeta de mer avancerade processerna inom produktutveckling som ständigt pågår i Fritid & Vildmarks verkstad. Deras mål har alltid varit att vara uppdaterade och anstränga sig extra för att presentera produkter utefter kundernas olika behov. När verkstaden skissade på en ny kolvmodell var det ett par angelägna faktorer som behövde beaktas – nämligen vikten och kostnaden. Följaktligen skulle toleranserna absolut inte påverkas till det sämre. Att produkten behövde 3D-printas var uppenbart för Moritz, som tidigare har varit med och utvecklat aluminiumprofiler där vissa anslutningar kunde konstrueras och tillverkas tack vare 3D-printing:
– Jag kom i kontakt med 3DVerkstan tack vare den produktutveckling vi bedriver på Fritid & Vildmark. Vi behövde en stabil och pålitlig partner för att kunna förverkliga våra idéer. Efter att vi analyserat olika firmor som erbjuder 3D-tjänster kändes valet självklart då ni kunde erbjuda mycket mer support än bara självaste utskriften.
En utmaning med 50 % viktreducering
Den stora utmaningen låg i att nå kravet gällande vikt med bibehållen styvhet och tålighet i produkten. När det handlade om att komma fram till rätt materialval, var det dessutom viktigt att resultatet skulle ha perfekt passform med minsta möjliga efterbearbetning. Patrik Rosén, applikationsexpert på 3DVerkstan, berättar om processen:
– Moritz behövde få hjälp med att få en produkt tillverkad som behövde bli cirka 50 % lättare än vad den var med dåvarande tillverkningsmetod. Vi 3D-scannade en handgjord referensmodell, och använde sedan mjukvaran nTopology för att skapa en lattice-struktur för delar av produkten. Detta för att lätta delen så mycket vi behövde för att nå den totalvikt som krävdes. Tillverkningen simulerades hela tiden för att vi skulle vara säkra på att vi hamnade på den vikt som krävdes.
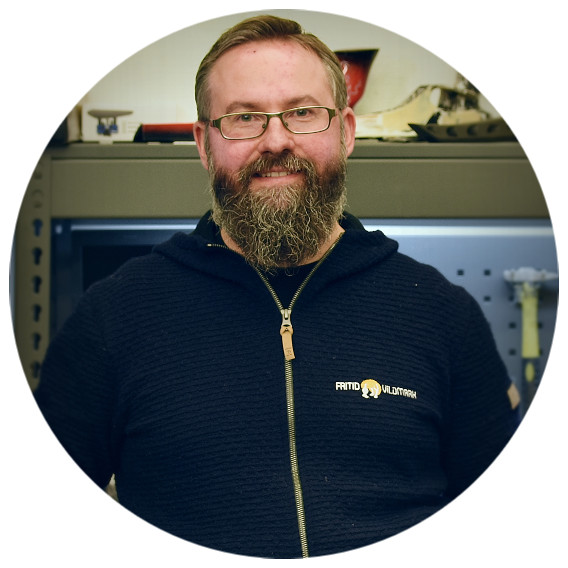
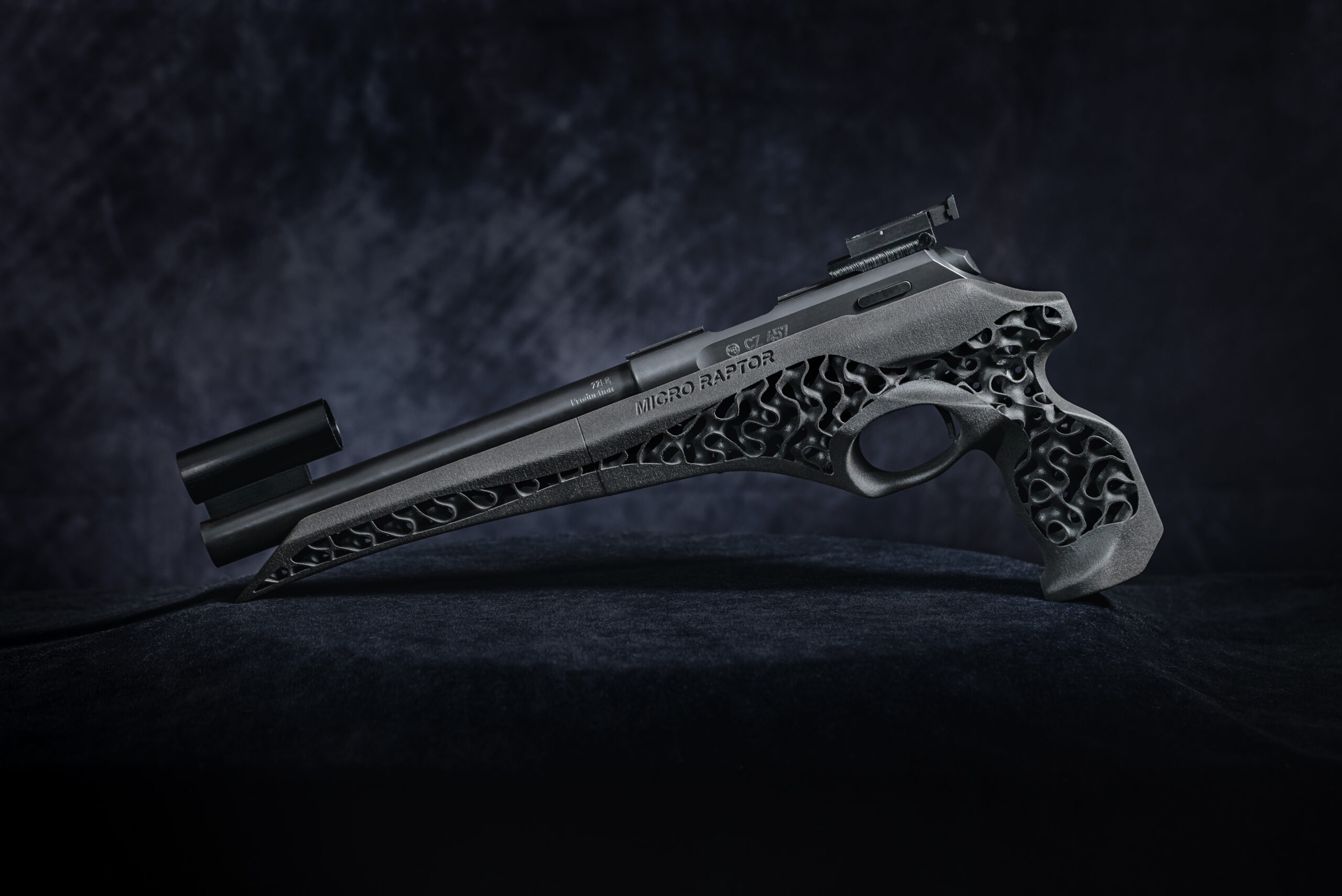
Övre bild: Moritz Isaksson. Nedre bild: Slutgiltiga kolvmodellen Micro Raptor. Lattice-strukturen möjliggör en lättare produkt, utan att tumma på funktionalitet.
Slutprodukten skrevs ut i Nylon 12
Produkten producerades slutligen i en mindre serie med hjälp av Formlabs 3D-skrivare Fuse 1 i Nylon 12 (PA12) – ett material med utomordentlig tålighet och ytfinish. Tack vare SLS-tekniken kan man skapa komplexa geometrier utan behovet av stödstrukturer – vilket möjliggjorde utskrift av lattice-konstruktionen som var väsentlig för att hålla nere vikten. Slutprodukten blev en kolvmodell som uppfyllde alla Moritz krav. Han avslutar:
– Resultatet överträffade förväntan och supporten från 3DVerkstan var på högsta nivå. De såg till att vi nådde mål på ett smidigt och professionellt sätt och kontakten var väldigt, väldigt bra.
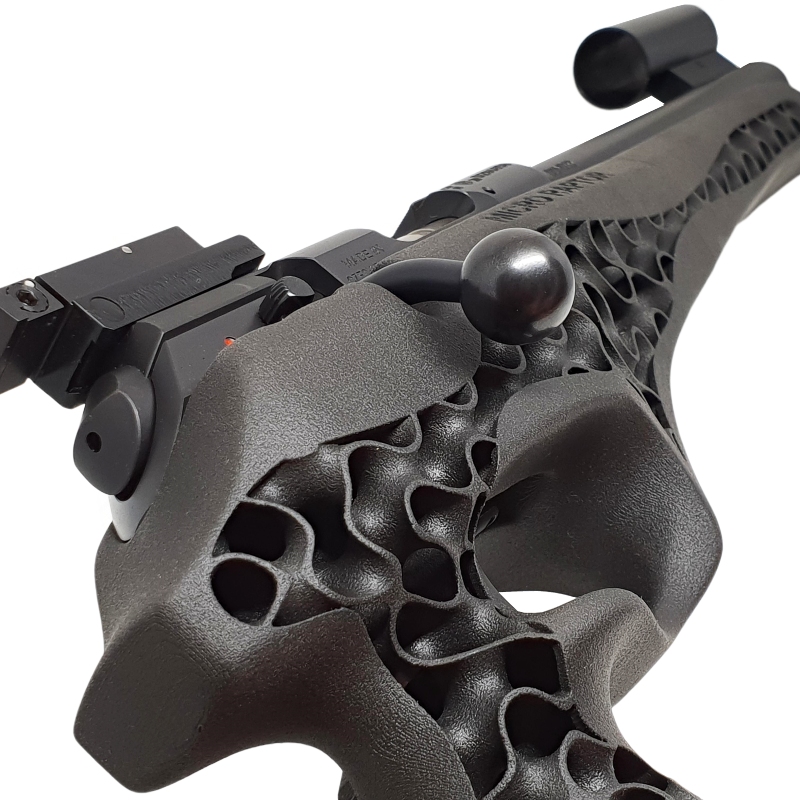
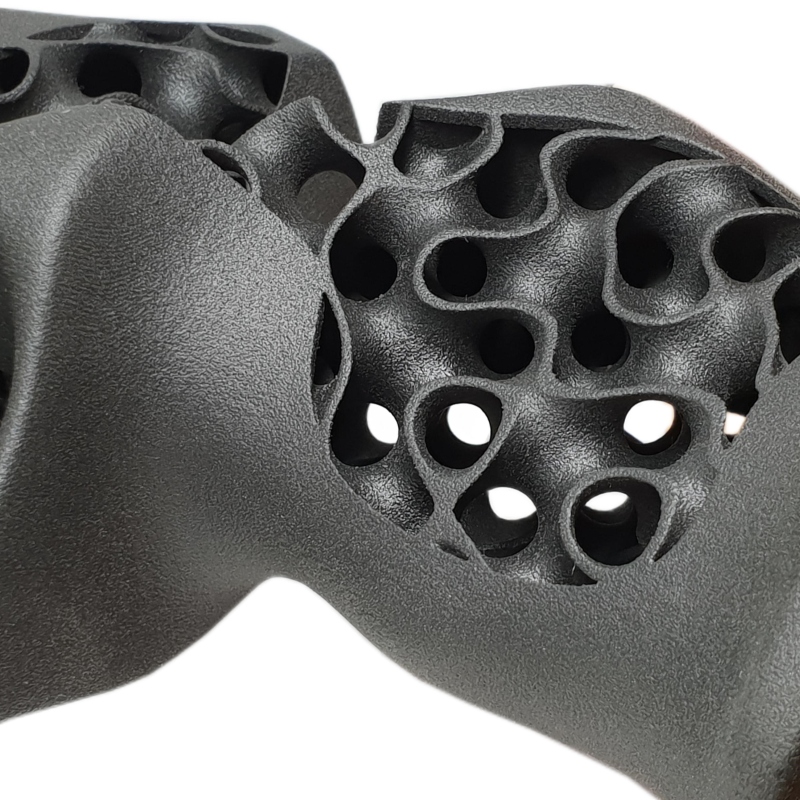
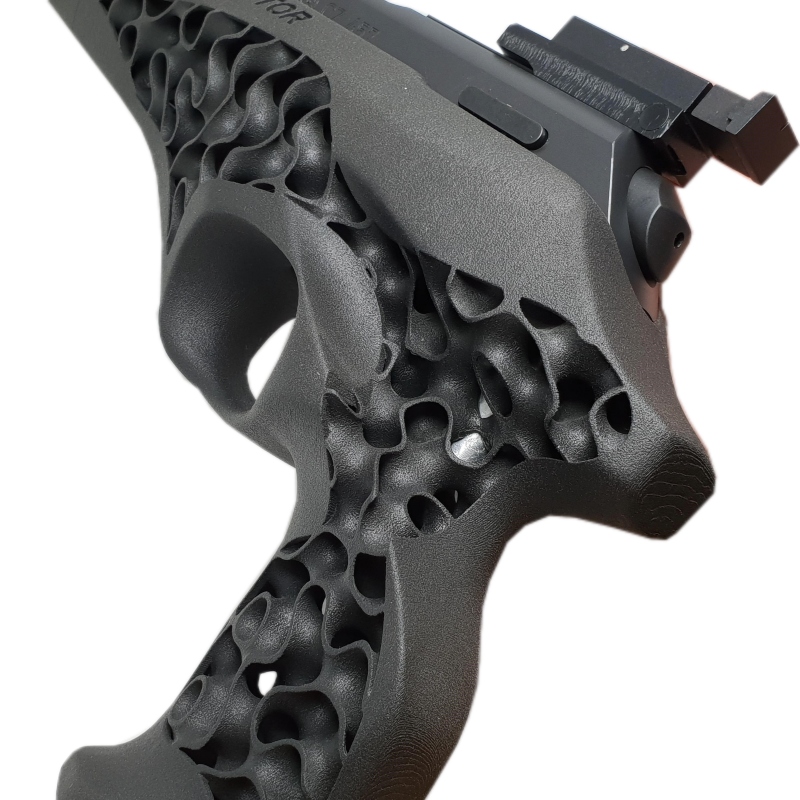
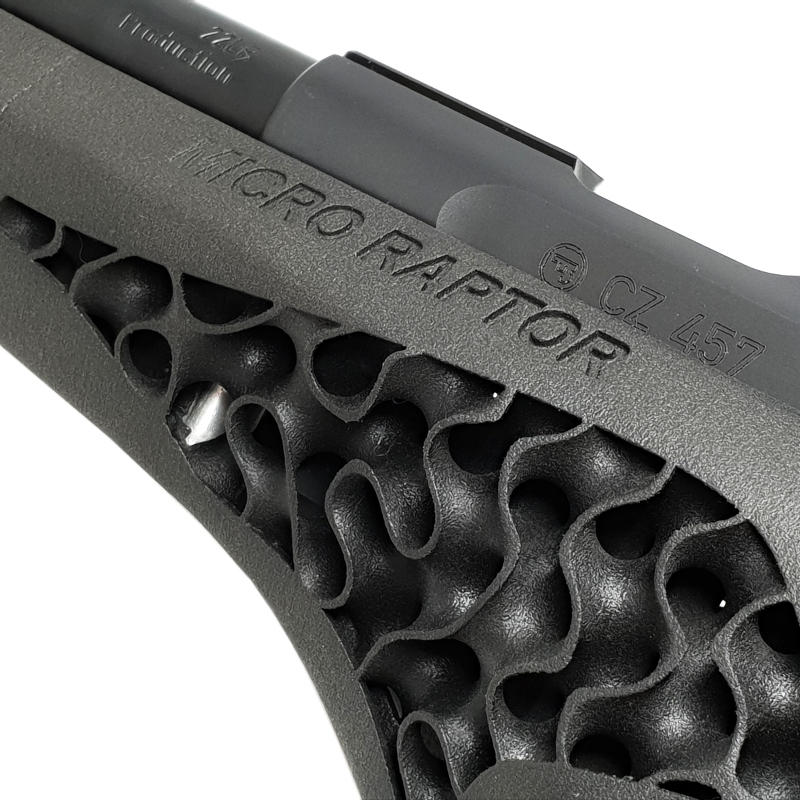
KONTAKTA OSS
Vill du veta mer om våra tjänster eller har du andra frågor? Fyll i dina uppgifter nedan så återkommer vi snarast.